ABS luggage from ABS particles (Acrylonitrile Butadiene Styrene) to the complete production, can be roughly divided into the following main steps:
1. Material preparation
ABS resin granules (particles): this is a thermoplastic with good toughness, impact resistance and processing performance, commonly used in the production of hard shell luggage.
Other auxiliary materials: such as masterbatch (for coloring), reinforcing agent, etc..
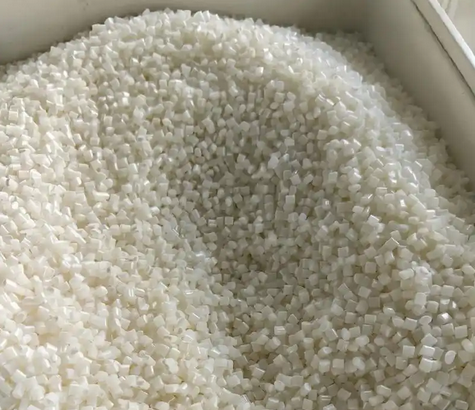
2. ABS sheet extrusion (sheet molding)
Drying treatment:
ABS particles contain a certain amount of moisture, need to be dried in the dryer (usually at a temperature of 80 ℃ –100 ℃, time 46 hours).
Extrusion sheet making:
The dried ABS particles are heated and melted through the sheet extruder;
Through the die extrusion to form ABS sheet;
Cutting after cooling and set aside.
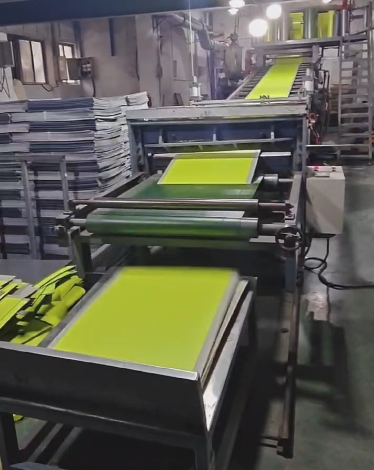
3. Plastic absorption (thermoforming)
Heat the sheet:
Put the ABS sheet into the blister molding machine, and make it softened by heat through the heating plate.
Mold suction molding:
Adsorb the softened sheet onto the mold to form the box shell shape (divided into upper and lower cover) by using negative pressure vacuum.
Simultaneous cooling and molding.
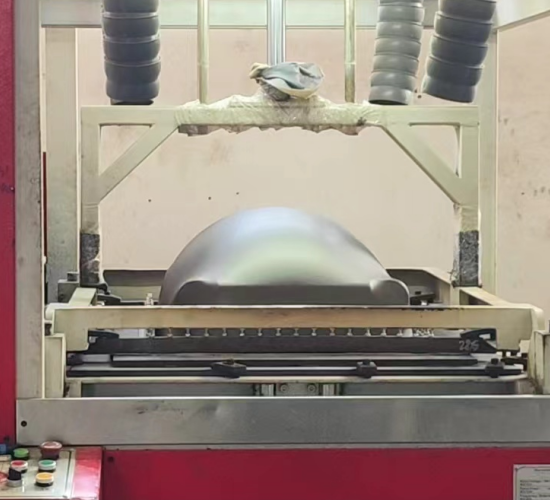
Trimming and Cutting:
Use automatic or manual way to cut off the excess part of the edge of the case to get a neat case.
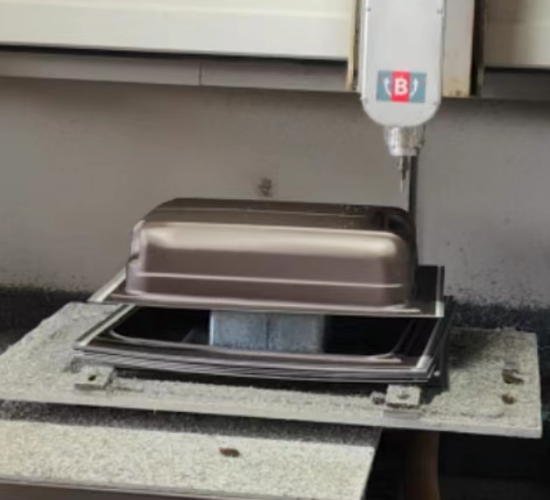
4. Shell processing
Punching/slotting:
Open screw holes, lever holes, caster holes, anti-theft zipper slots and so on.
Installation of metal reinforcement strips (if any):
Some designs will add metal edge strips to strengthen the structure.
Painting/Laminating (optional):
Surface treatment of the case shell, such as oil spraying, labeling, anti-scratch pattern treatment, etc.
5. Hardware Installation
Installation of trolley bar system (aluminum alloy or iron telescopic trolley bar)
Installation of universal wheel
Installation of handles and side handles
Installation of combination lock or TSA customs lock
Installation of zipper or hinge system
Installation of lining cloth:
Stick the pre-made lining cloth into the box and sew or paste it.
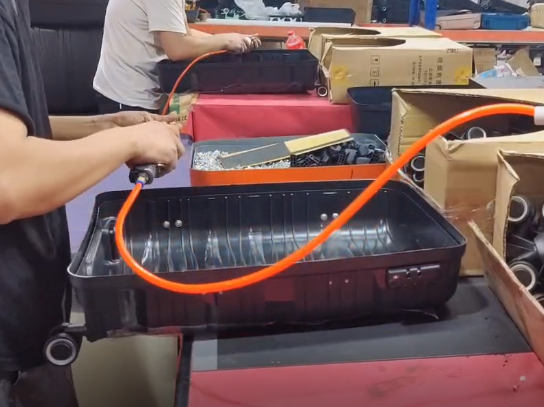
6. Quality Inspection
Check the box flatness, wheel rotation, trolley rod expansion and contraction, lock function, and overall structural firmness.
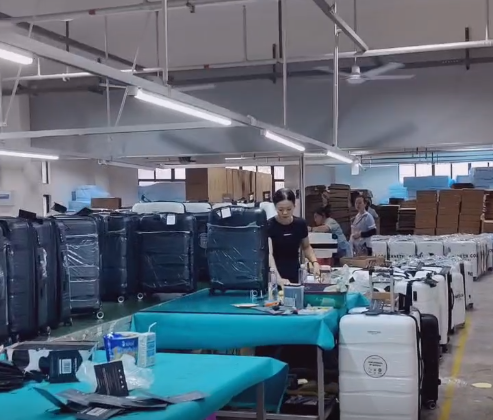
7. Packaging and shipping
Wipe clean → put into poly bag → outer box → shipment.
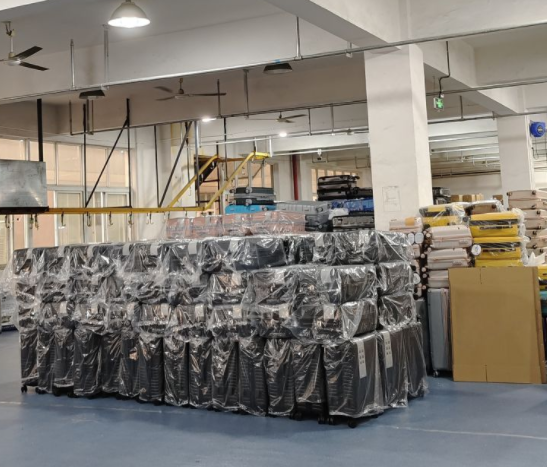